Examine This Report about Inventory Management
Wiki Article
All About Inventory Management
Table of ContentsRumored Buzz on Inventory ManagementInventory Management Things To Know Before You BuyMore About Inventory ManagementThe Best Guide To Inventory Management
There are two main methods of maintaining track of inventory: periodic as well as perpetual. The primary difference in between these is exactly how typically data is upgraded. No matter just how commonly you track inventory, you may intend to utilize among the adhering to stock administration strategies: ABC Evaluation, ABC (Always Better Control) Analysis is stock administration that separates different things into three classifications based upon prices as well as is divided right into teams A, B, or C.The items in the B category are reasonably cheaper contrasted to the A group. And also the C group has the least expensive items of all 3. EOQ Design, Economic Order Quantity is a strategy made use of for planning as well as buying an order quantity. It entails making a decision relating to the quantity of stock that should be placed in stock at any kind of provided time. Inventory Management.
FSN Technique, This technique of inventory control describes the procedure of monitoring all the products of supply that are not made use of regularly or are not needed all the time. They are after that classified into three different categories: fast-moving inventory, slow-moving inventory, and non-moving inventory. JIT Technique, Simply In Time inventory control is a process made use of by makers to manage their supply levels.
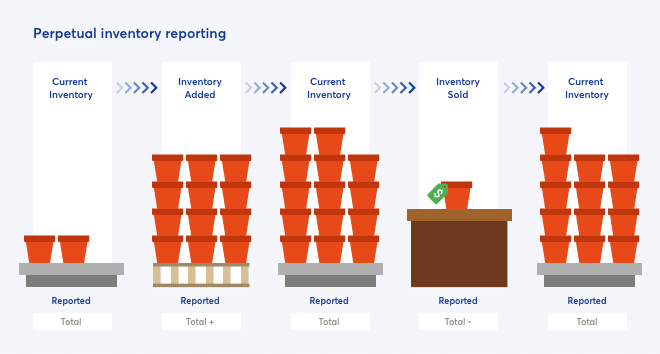
How Inventory Management can Save You Time, Stress, and Money.
VED Evaluation, VED is a strategy utilized by organizations to control their inventory. It mostly relates to the administration of important as well as preferable extra parts. The high degree of supply that is required for production typically justifies the low inventory for those parts. Among the most essential elements that a company need to consider is the precision of the details offered in its stock databases.Wrike is a job administration remedy that can assist you do precisely that. With Wrike's item management tools, you can handle all of your item group's activities in one location and get one of the most out of every project. Wrike's product launch automation aids speed up item launches with a streamlined method.
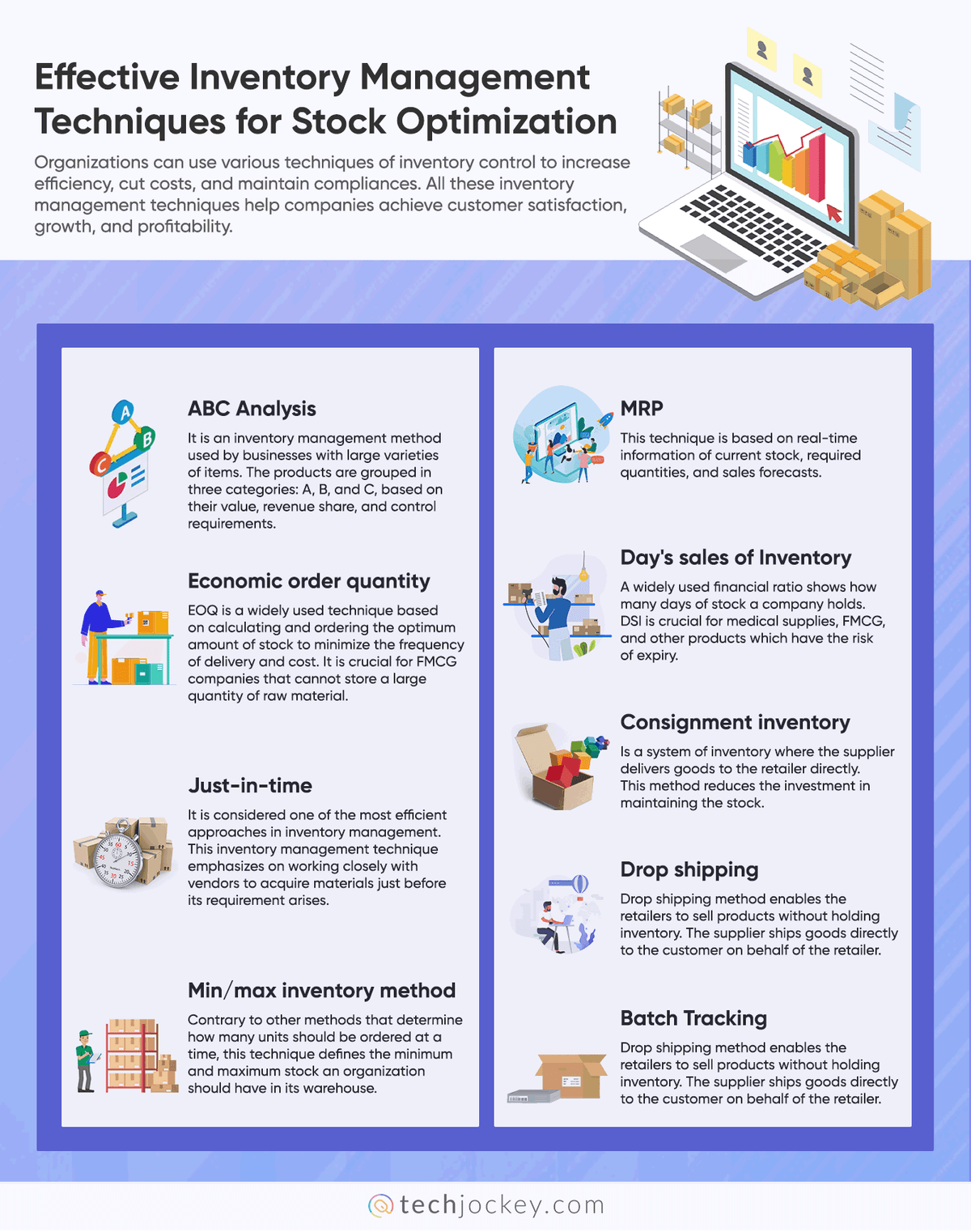
:max_bytes(150000):strip_icc()/inventory-management-8595e839c2884128997ca77f00a8da2b.jpg)
Supply management tries to efficiently enhance stocks to prevent both gluts and also scarcities. 4 significant stock management techniques consist of just-in-time monitoring (JIT), products demand planning (MRP), financial order amount (EOQ), and also days sales of supply (DSI).
A lack of inventory when and where it's needed can be extremely detrimental (Inventory Management). At the exact same time, inventory can be considered an obligation (otherwise in an accounting feeling). A huge supply brings the risk of putridity, burglary, damages, or changes popular. Inventory has to be insured, and also if it is not offered in time it may need to be thrown away at clearance pricesor just destroyed.
Recognizing when to restock stock, what total up to buy or generate, what price to payas well as when to offer and at what pricecan conveniently become facility choices. Local business will usually monitor supply by hand and establish the reorder points and amounts utilizing spreadsheet (Excel) formulas. Bigger organizations will utilize specific enterprise source preparation (ERP) software program.
The Inventory Management PDFs
Ideal supply management techniques differ depending upon the industry. An oil depot is able to save large quantities of inventory for prolonged durations of time, permitting it view it to wait for need to pick up. While keeping oil is expensive and also riskya fire in the U.K. in 2005 brought about numerous pounds in damages as well as finesthere is no threat that the inventory will certainly ruin or head out of design.For firms with complicated supply chains and producing processes, stabilizing the threats of supply excess and lacks is particularly difficult. To accomplish these balances, companies have created several methods for inventory management, including just-in-time (JIT) as well as products demand planning (MRP). Some companies, such as financial solutions firms, do not have physical stock as well as so should depend on service procedure monitoring.
Inventory has to be physically counted or determined before it can be placed on an equilibrium sheet. Firms typically keep innovative inventory monitoring systems capable of tracking real-time supply levels. Stock is represented utilizing one of three approaches: first-in-first-out (FIFO) setting you back; last-in-first-out (LIFO) setting you back; or weighted-average setting you back. A supply account normally contains four separate groups: Basic material stand for different materials a company purchases for its production process.
Operate in procedure (also known as goods-in-process) stands for raw products in the procedure of being changed into a completed product. Ended up goods are finished items conveniently available available to a company's consumers. Goods represents finished products a company gets from a distributor for future resale. Depending on the sort of company or item being assessed, a firm will certainly utilize numerous supply management approaches.
Report this wiki page